Workplan: Hand and Power Tools
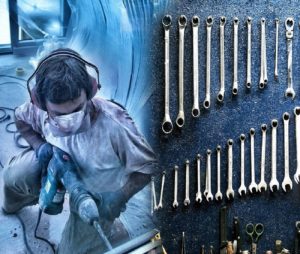
Cuts and other hand injuries to the hands are one of the most frequent and common injuries workers face. Hand injuries, including amputations, can keep workers away from the job for several days and can cost employers big money. But they are a preventable and avoidable risk to employees and cost to employers.
Step 1: Tool Assessment
Take stock of the types of tasks, jobs, and operations that require the use of hand or power tools. Are these available and in good working condition? Are workers using the right tools for the work they are performing? Do they need a different tool? Would a power tool lessen the repetitiveness or force needed to do the job?
Step 2: Hazard Assessment
Conduct a hazard assessment wherever hand or power tools are used. The assessment should identify sources of hazards that could expose employees to flying objects, shock or electrocution, sparks, punctures, cuts, and crushing forces. Each hazard assessment will identify hazards, recommend controls, and provide guidance on appropriate personal protective equipment (PPE) selections when a hazard can’t be eliminated.
Step 3: Hazard Controls
Remove or eliminate the hazard whenever possible. If that can’t be done here are some examples of hazard controls for tool use. Ensure power tools are fitted with guards and safety switches. Provide PPE to protect against flying objects, dust, or and enforce its use. Use caution with gloves and prohibit their use when using powered equipment if there’s a chance the glove could get caught.
Establish and enforce a housekeeping schedule that includes keeping workplace floors as clean and dry as possible to prevent accidental slips with or around dangerous hand tools.
Implement an ergonomics program for hand and power tools to prevent repetitive motion and other ergonomic-related injuries. Refer to the Selecting Hand Tools and Checklist for the Hand Tool Selection Checklist for additional information.
Step 4: Establish Inspection Procedures
All tools should be inspected before use. Look at handles, tool edges, power cords, hoses & connections, switches, triggers, casings, and attachments. Check hand tools for cracks dings and chips. Don’t use damaged tools. Generally, hand tools cannot be repaired and should be thrown away. Power tools should only be repaired by someone trained and qualified to make repairs checklist templates you can use as-is or edit.
Step 5: Establish Maintenance and Safe Storage Requirements
Tools must be kept clean, sharp, and well-maintained to be used safely and effectively. Set up areas where tools will be protected from the elements and damage from other tools and equipment. Make sure workers know how to safely sharpen knives and blades and when to sharpen them.
Here are some additional maintenance and storage items to implement:
Clean tools after use. Wipe down with a rag or towel to remove dirt, grease, and debris. As you are cleaning, check for damage or defects. If the tool cannot be repaired, tag it and dispose of it. Clean metal surfaces with an approved solution and scrape away any soil and dirt. Completely dry the tool with a towel or rag before it is placed in storage. Coat the metal parts of the tools with a lubricant.
Don’t place tools directly on the ground for storage. Place small hand and power tools on shelving. Store short-handled tools in a plastic bin or box. Tie together long-handled tools in a bin or hand them on the wall. Power tools should have all surfaces cleaned and completely dry before storage. Spray lubricant on all metal surfaces. https://www.ezstorage.com/blog/how-store-hand-and-power-tools/
Step: 6 Training
- Ensure employees have been trained and fully understand operations and maintenance procedures and safe tool use.
- Provide employees with the right PPE and train them how to use and care for it.
- Educate workers on the dangers of loose or baggy clothing, long hair, and jewelry. Long hair must be pulled back and the safest bet is to remove all jewelry before using tools.