Farm Workshop Safety Talk
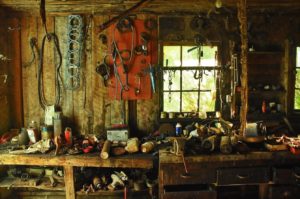
WHAT’S AT STAKE?
The workshop is essential to the operation of our farm. There are a wide variety of work tasks that happen in the shop and there is the potential for many hazards. A tidy, organized workshop is important to safe and effective work.
WHAT’S THE DANGER?
HAZARDS IN WORKSHOP
People working in the farm workshop are exposed to risk of injury and illness associated with a range of hazards. Up to 20% of farm injuries presenting to hospital Emergency Departments are caused by farm maintenance work. More than 30% of these are eye injuries and more than 30% are hand injuries.
Hazards Include:
- Poor workshop design and layout
- Electricity
- Welding
- Oxyacetylene welding and cutting
- Grinding
- Using power hoists
- Using power and hand tools
- Battery charging
- Tire changing
The types of injury range from death, serious injury requiring hospitalization and down time, to “nuisance” injuries that stops work for a short time, or makes work slower and reduces productivity.
HOW TO PROTECT YOURSELF
GOOD SHOP MANAGEMENT CAN PREVENT INJURIES AND IMPROVE THE EFFECIENCY OF REPAIR OPERATIONS.
Keep it Clean
- Many injuries are the direct result of poor “housekeeping” in the workshop. Trips, slips, and falls account for the bulk of these mishaps.
- Scrap material and wrappings, loose parts, scattered tools and equipment, and oil spills all pose hazards. Oil spills should immediately be covered with absorbent material and cleaned up promptly Debris should be swept up and disposed of in designated containers.
- Parts should be kept on the workbench. Tools should be placed where they cannot fall and cause damage or injury.
Lighting, Heating, Ventilation
- Windows and overhead lighting are essential to provide a good level of overall illumination. Additional lighting should be available over work benches and stationary tools.
- Supplemental heating is required for winter shop work. The heating unit should be located to provide adequate, even distribution of heat. Ceiling heaters leave the work area clear.
- Open doors and windows may provide adequate ventilation of smoke, fumes and exhaust gases in the summer. Special systems may be needed to remove exhaust fumes and other gases during cold weather months.
- Flexible pipe or tubing can be used to vent exhaust gases. Properly designed ventilation systems are required in welding and battery areas to remove smoke and fumes. A booth with separate venting is recommended for paint fumes.
Electricity Safety
- Wiring must be of adequate capacity to handle lighting, heating and power tool requirements.
- The shop should have a sufficient number of conveniently located outlets.
- Conductors, plugs and receptacles should all be 3-wire grounded to prevent shock with power tools.
- Sufficient power should be available for welders and motors used in the workshop.
- Welding and grinding equipment.
- Power tools – checking guards and cords.
- Hoists used to work on farm vehicles.
- Poor lighting – leading to accidents.
Ground fault circuit interrupters (GFCI’s) are recommended for wash bays and other damp areas. Explosions-proof wiring, motors and fixtures are required were flammable gases, fumes, or vapours may be encountered.
SHOP MANAGEMENT OVERVIEW
- Keep all tools and service equipment in good condition.
- Always use the appropriate personal protective equipment for operations such as welding and grinding.
- Keep floors and benches clean to reduce fire and tripping hazards.
- Clean the area completely after a job is finished.
- Empty trash containers regularly. Never store oily, greasy rags in closed containers – this practice has been responsible for numerous fires due to spontaneous combustion.
- Lighting, wiring, heating, and ventilation systems should be properly maintained.
- Do not allow unauthorized use of tools, service equipment and supplies.
- Don’t allow anyone to use tools or service equipment without proper instruction.
- Keep guards and safety devices on power tools in place and functional.
- Use tools and service equipment only for their designed purpose.
- Service fire extinguishers on a regular schedule.
- Keep the first aid kit fully stocked.
WORKSHOP SAFETY CHECK
- keep the workshop tidy and avoid tripping hazards such as trailing cables, tools etc;
- welding gas bottles are secured upright, and when in use can be moved easily on a trolley;
- battery charging is done in a well-ventilated area away from sources of ignition such as welding flames or angle grinding;
- avoid chlorinated solvents such as ‘trike’ or ‘perc’ for degreasing. Use a less harmful product (not paraffin or petrol) and put degreasing baths in well-ventilated areas;
- arc welding is done in a protected area so that others nearby are not affected by the ultra-violet light and suffer ‘arc-eye’ as a result;
- use the correct abrasive wheel for the job and adjust bench grinder tool-rests close to the wheel;
- escape from inspection pits easily and that inspection lamps have protected bulbs (flammable fluids such as petrol may collect in the bottom of the pit and explode with the heat from a broken bulb filament);
- noise levels from plant such as compressors are controlled – site the machine in a separate closed area or outside;
- hand tools are in good condition and suitable for the job;
- PPE is provided – eye protection for chiseling, grinding and welding work; respiratory protection for work that creates dust, if extraction cannot be provided; or foot protection if there is a risk of things falling onto the feet;
- electrical installations and equipment are maintained in good condition, regularly inspected and tested;
- safe means of access is provided for raised storage areas or mezzanine floors;
- lifting equipment and mechanical handling aids are used to reduce risk of muscular skeletal injury (MSDs) eg when moving heavy machinery components. Such equipment should be capable of handling the required loads and be regularly inspected and tested. Lifting equipment will also require thorough examination.
- work at height can be carried out safely. Mobile tower scaffolds can be used as working platforms and may be safer than using a ladder for some tasks.
9 FARM WORKSHOPSAFETY TIPS
- Prevent falls. Good housekeeping is fundamental. That means sweeping walkways and work areas, and cleaning up grease, gasoline, and water spills. Trips and falls are caused by clutter, especially extension cords.
- Improve lighting. For general office and shop work, aim for 50 foot-candles of illumination. For detailed bench work or specific office desk work, use 100 foot-candles. For general machinery storage, 3 to 5 foot-candles is adequate.
- Use hoists, cranes, and lifts. Over half of back injuries occur from lifting. Hydraulic lifts and hoists can help to reduce these injuries.
- Wear protective equipment. Personal protective equipment should be used from head to toe, starting with shoes or boots with a heavy tread.
Wear earmuffs in the shop. They’re easy and quick to put on and take off.
Respirators filter dust, paint fumes, gases, or other hazardous material. Use NIOSH-approved filtering face pieces: N95, N100, or P100.
Leather gloves, chemical-resistant gloves, hard hats, protective aprons, and welding shields are vital. Goggles with side shields protect against chemical splashes, dust, fumes, and debris from bench grinders. Wear a NIOSH-approved respirator that fits under a welding hood, such as a 3M Particulate 8233 or a Moldex 2400 N95 or 2800 N95.
- Prevent electrical injury. Make sure that electrical equipment is properly grounded. If an electrical tool isn’t double insulated, there must be a third prong for grounding.
Driving over extension cords creates shorts. Frayed cords are a shock hazard. You shouldn’t use less than 12-gauge cords. The heavier ones cost more, but they’ll power every piece of equipment and pose less risk of motor damage. Heavier-gauge cord won’t overheat or be a fire hazard.
Most farms don’t have conduits for wiring, so electrical wires are exposed. Sometimes you take things outside to work on, and shocks are a hazard if it’s damp.
- Prevent fires. Flammable and combustible materials should be stored away from heat sources, and flammable liquids should be kept in covered containers. Fire extinguishers should be hung by the shop door. It is recommended to use a 20-pound ABC extinguisher for shops. Check your extinguishers annually.
- Improve ventilation. Ventilation is vital in a heated shop. Engineering controls are the best way to remove air contaminants, with a ventilation system that includes hoods, roof vents, and high-speed intake and exhaust fans.
An exhaust fan must move 1,000 to 2,000 cubic feet of air per minute to completely remove welding fumes. For engine fumes, fans must be capable of moving 250 cubic feet per minute per vehicle. “Welding or cutting needs to be done in an area with exhaust fans to take fumes up and out,” Grafft says. “You’ll know it’s designed correctly if the fumes draw down and away from your face when you’re welding.”
- Safeguard storage loft. A railing and stairs help prevent falls.
- Use bulk lubricant storage. Avoid skin contact with oil and solvents. Complete containment eliminates spills and slick spots on the shop floor. Oil should flow from the bulk container through a hose and past valves in a three-way valve junction.
FINAL WORD
The farm workshop can be the scene of many injuries. Many of these injuries involve hands or the eyes. Other injuries involve burns, cuts, abrasions and sprains to various parts of the body.